The Carron Cupola magazine ran profiles on the people who worked for the Carron Company. Read their stories to find out what it was like for men, women, and children at the ironworks.
Nurse Marshall could see up to 60 patients on a daily basis.
if ($section->fields['text']) echo $section->fields['text']; ?>
William Inglis: Low Foundry Worker
William Inglis was an assistant to the manager in the Low Foundry, and was from a family steeped in the Carron Company, saying “Moulding seems to be in our blood.” He added:
My father, grandfather and great grandfather spent their lives working at Carron. Together our time adds up to more than one hundred and fifty years’ service.
if ($section->fields['text']) echo $section->fields['text']; ?>
Considering that William was interviewed for The Cupola in 1952 his family history at the Carron Company stretched across the 18th, 19th and 20th centuries! William’s first recollections of the Carron Company were at the age of 8 years old. He fondly remembers being lifted over the walls of Forge Row en route to the works with his father.
William worked across the vast range of departments at Carron, from stoves to baths, pillar-boxes to radiators. He eventually worked his way through the plate shop and up the company ladder to become the Pattern Moulders Foreman in the Low Foundry. Away from the grind of the works, William spent his time as a young man playing football and golf before retiring to spend more time in his garden. These were not uncommon past times for employees of Carron.
Robert Lorn: Moulder, Heavy Foundry Department
In 1951 Robert Lorn had worked for Carron for sixty-six years. He was 11 when he started with the company as a message boy in C warehouse. At 13 he moved to the Time Office, and moved from there to the Engineering department. After one year there he transferred to the Heavy Foundry. He was the third generation of his family to work for Carron Company.
Robert Lorn worked as a loam moulder. Loam is composed of equal parts of sand, silt and clay. The loam is applied with bare hands to ensure even packing between the mould joints. This loam will allow hot gases to escape from the mould as it’s filled with molten metal. Robert Lorn also made sand moulds. He made the plant, core irons, and gratings for the various jobs that were being moulded in the shop. He would make sure the sand was perfectly level over the bed and then stamp out shapes of the parts to be moulded. Once stamped he would insert a dapper at various points. This meant gratings made by the stamp would stand on legs or prongs which had been made with the dapper. Apparently, this operation is comparable to transplanting a bed of leeks. In recognition of his long service, Lorn received a lovely little watch which was just what he wanted.
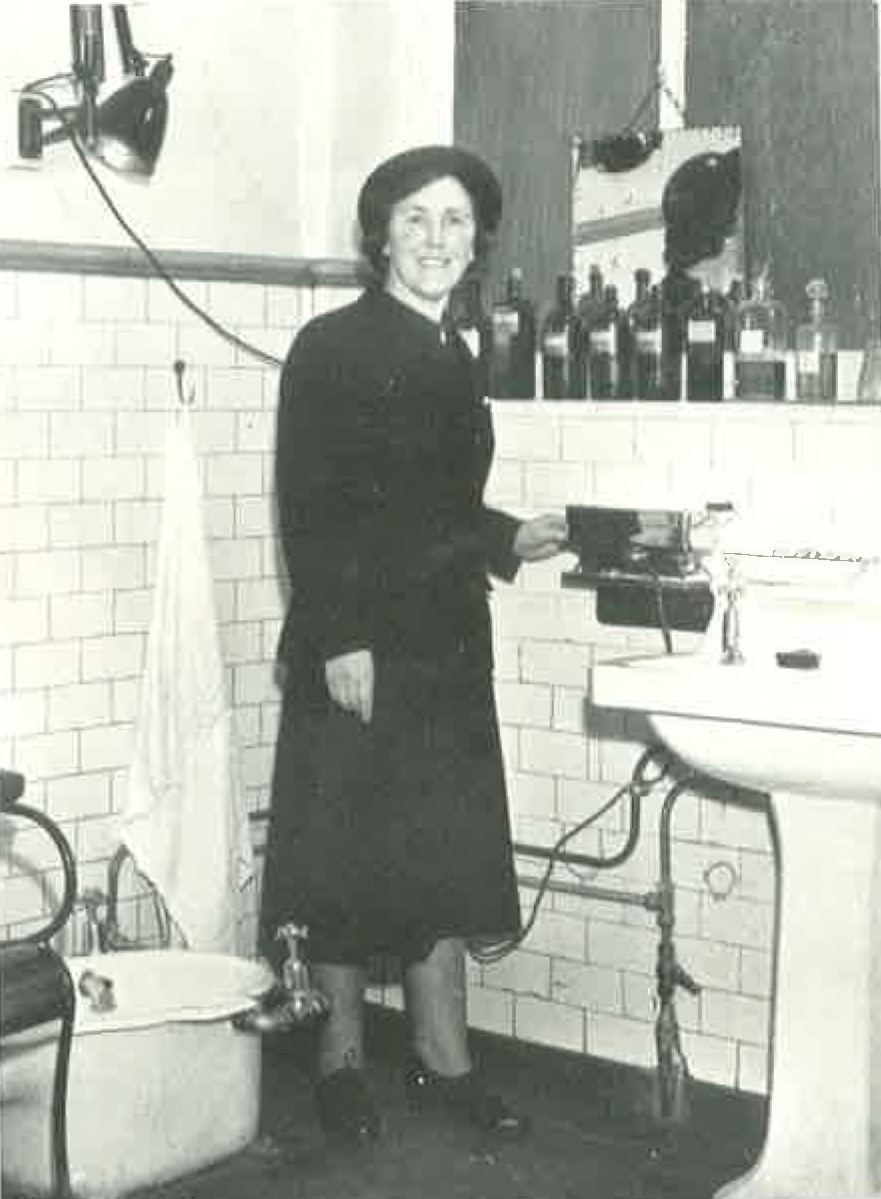
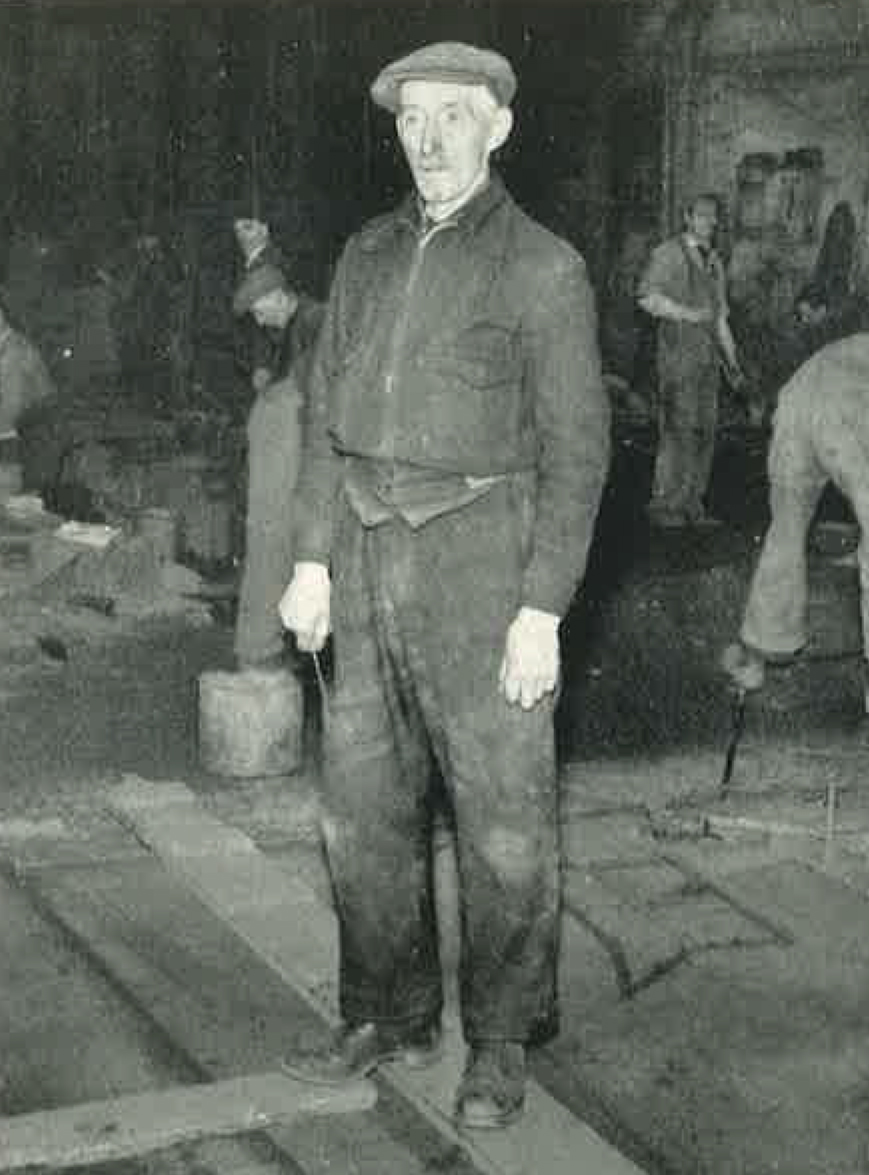
Nurse E. Marshall: Company Nurse
Before joining Carron Company, Nurse Marshall was a ward and theatre sister, and completed her nursing training at Glasgow Royal Infirmary. She started working for Carron in 1941. As an industrial nurse, she made sure she was conversant with all the industrial processes which Carron employees were involved in. She would visit both Mungal Foundry and the engineering department daily. She was also Welfare Supervisor for the women employees. Nurse Marshall could see up to 60 patients on a daily basis. Some of these patients would return daily to have bandages changed. The type of injuries she dealt with included burns, scolds, cuts bruises and eye injuries. Serious injuries didn’t occur frequently due to improvements made to machinery and in health and safety.
James Craig: Steam Locomotive Driver
James Craig started working for Carron Company aged 14 in the Foundry Moulding Department as an apprentice. He worked there until 1917 when he became a steam locomotive fireman. His father was already working as a railway shunter with the company. James’s steam locomotive served all the main section of the foundry including Low Foundry, Heavy Foundry, Mungal Foundry and the Engineering Department.
His day started at the Mungal Yard where he picked their quota of goods wagons delivered overnight by British Railways. The wagons contained all the goods necessary for the works to function, such as machinery, paint, wood, and fuels of various types. These wagons were then shunted over the weigh bridge where two clerks would note down the gross weight, tare, and number of each wagon. The tare (the weight of the empty wagon) was clearly written on each wagon. This meant the weigh clerks could subtract the wagon’s weight from the gross weight and work out the actual weight of the wagon’s contents. From here the wagons would be separated and shunted to the correct departments as per their labels.
The driver had to be constantly aware of what was happening around him. How would the train react if it was pulling only one or several wagons? How quickly would it stop if the rails were wet, dry, or greasy. What if someone appeared suddenly on the rails? A visiting Carron mine manger asked James Craig how he could possibly know all the rails and labyrinth of crossings throughout the Carron works. Craig replied that he knew them in the same way that the mine manager knew all the roadways in his mine.
James Watson Lawson: Despatch Warehouse Progress Clerk
James Watson Lawson worked for the Carron Company for over forty-four years (minus three years when he served in the army during the First World War). He was the fifth generation of his family to work for Carron; his great-great-grandfather on the maternal side of his family had come with other workers from Yorkshire to assist at the works. This was in 1759 when the works had first started. Lawson’s paternal great-great-grandfather had come over from Sweden in the 18th century to build boats in Carronshore. These boats sailed on the river Carron carrying goods from the works to Grangemouth. He could recall the first fire at the works which took place on 26th January 1887. Lawson could verify the date of the fire as it had been written on the office wall of one of the warehouses. This date was in the hand writing of Peter Rae who had worked for the company for over 67 years. You can see his story on this website.
By John McMorrine and Ian Fraser.